Bearing Lube Oil Systems provide the life blood to many bearings, gearboxes, and/or blowers – Lubrication Oil
- Kristen Modzelewski
- Jul 15, 2024
- 2 min read
Bearing Lube Oil Systems (also known as Circulating Oil Systems or Lube Oil Skids) are an integral and very important part of most rotating equipment used in many industrial applications around the world. Whether part of the rotating equipment itself or a separate stand-alone system designed by a third party, a Bearing Lube Oil System provides the life blood to many bearings, gearboxes, and/or blowers – Lubrication Oil.
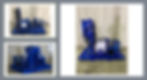
Each application for a Bearing Lube Oil System is unique and requires precise oil flow, pressure, and temperature to be delivered to one or more bearings, in order to meet the OEM specification of the bearing(s).  At Oil Filtration Systems®, we have the engineering and real-world experience to help properly design and manufacture a Bearing Lube Oil System for you. Â
To ensure proper lubrication as well as to meet specified ISO cleanliness levels, we utilize high efficiency pleated microglass filter elements rated Beta>1000 to filter your oil and meet or exceed OEM cleanliness specifications.
We offer duplex pump/motor combinations for redundant oil flow protection, as well as duplex filter configurations to ensure uninterrupted oil flow to the bearings.
Air or water-cooled heat exchangers sized properly to reduce the temperature of the oil, which in turn carries the heat generated by the bearings away.
Properly sized oil tanks with or without baffles, designed to hold the total volume of oil and facilitate the best gravity feed from the bearings back to the tank.
Oil immersion heaters to heat the oil to desired temperature during cold startups, which lowers the viscosity of the oil to proper levels.
Digital and analog instrumentation (gauges, flow indicators, flow meters, oil level indicators, and much more) are typically added to make sure proper operation is achieved and observed.
Fully automatic control systems with alarms and functions can be added to limit the need for constant monitoring and can also be integrated into your DCS for remote monitoring.
We also offer units built to meet Class 1, Division 2 and Class 1, Division 1 hazardous location ratings.